In-line cooling uses 50% less electricity, cools milk faster
Milk leaves a cow's body at 98° Fahrenheit and needs to be cooled
quickly to less than 40°. Knowing this, it is easy to believe that milk
cooling makes up about 18 percent of a Wisconsin dairy's total energy costs.
By installing an in-line plate cooler, milk temperature is lowered before entering
the bulk tank to be cooled further. This technology has proven its worth for two
decades, and recent studies find it can reduce cooling costs by almost 50 percent.
In-line cooling also cools milk faster, which helps lower bacteria counts and is
easier on the compressors. An in-line milk cooler is one of the best investments
you can make in your dairy operation.
Less electricity is used
By partially precooling milk before it hits the refrigerated bulk tank, the bulk
tank compressors don't need to work as hard to cool milk down to storage temperature.
In fact, in-line cooling has been found to cut the electrical cost of cooling
milk by almost 50 percent. This savings is possible because milk is precooled up
to 30° or more, requiring that the compressors run approximately 10 to 15
minutes. Conventional cooling, in which all cooling is done in a bulk tank,
requires that the compressors run approximately 30 to 45 minutes to cool the
milk.
Enhance your dairy's bottom line by using less electricity while milking.
Simply by using well water to partially cool milk prior to entering the bulk
tank, an in-line cooling system can pay for itself in two years.
A recent study found that almost any size dairy can cut its electrical use
for milk cooling by almost 50 percent with in-line cooling. Milk cooling is one
of the largest energy draws on a dairy, so this could mean big savings. A
different study looked at total annual energy savings from in-line cooling
for different size dairies. It found that the larger the dairy, the more in-line
cooling can reduce the total annual electric bill. This makes sense because the
larger the dairy, the more milk cooling is done, and the savings potential is
greater.
Number of cows |
Reduction of total energy use due to processing |
kWh/yr reduction |
60 |
15% |
3,500 kWh/yr |
200 |
25% |
11,400 kWh/yr |
400 |
29% |
22,500 kWh/yr |
R.W. Peebles, D.J. Reinemann, R.J. Straub, Presented as ASAE
Paper No. 93-3535.
Back to top
Milk is cooled faster
In-line precooling significantly reduces cooling and agitation time. When
precooled milk is pumped in, the bulk tank compressors finish the cooling in only
10 to 15 minutes. Faster cooling increases the capacity of the bulk tank because
a higher volume of milk can be cooled at once. Without precooling, a large volume
of warm milk poured too quickly into the tank makes it difficult to cool the milk
and keep it cool-especially when warm milk is blended with cooled milk. In-line
cooling also reduces the wear and tear of the cooler's refrigeration system by
giving it a big head start.
Back to top
Improves milk quality
Improper milk cooling is one of the leading causes of high bacteria counts in
milk. The faster milk is cooled once it leaves the cow, the better: storage below
40 degrees stops or substantially reduces most bacterial growth. In-line cooling
uses well water to cool milk by 10, 20 or 30 degrees or more before it enters the
bulk tank, enabling the compressors to finish cooling the milk in less time. Dairy
operators using in-line cooling can be assured that their milk meets these temperature
regulations:
- Milk pumped into the bulk tank should be cooled to 50 degrees within the
first hour and to 40 degrees within the second hour
- Milk added at subsequent milkings should not raise the temperature of the total
milk in the bulk tank to above 40 degrees
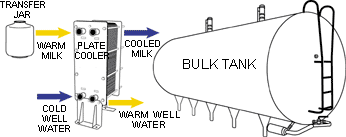
Back to top
In-line technology is proven
In-line milk cooling is not a new technology; it has been gaining in
popularity on dairy farms for two decades. In-line coolers are typically
installed between the transfer jar and bulk tank. A widely used in-line
cooler design is in the form of a plate cooler. In-line plate coolers run
well water and milk in opposite flow channels over a series of metal plates.
Milk is cooled as its heat is transferred to the cool water on the opposite
side of each plate. Depending on the system, in-line plate coolers can drop milk
temperature by 30 degrees or more. Variables include the temperature of the well
water, the ratio of water to milk in gallons per minute, and how many times the
milk passes the cold-water channels. There are many sizes of plate coolers available
to fit any size dairy: from stanchion barns to double-50 parlors.
Back to top
Warmed water can be reused
In-line cooling has been called "virtually free cooling" because the well
water used to cool milk would have been used anyway for the livestock or barn
chores. The warm water resulting from milk cooling can easily be used to water
livestock, heat the milk room or perform other chores. One idea is to pipe the
water to a tank in the holding pen so cows have warm, fresh water while they
wait to be milked. Since cows prefer warm water to cold, they may drink more
water and, subsequently, produce more milk.
Back to top
Variable-speed pump teams well with in-line cooling
Variable-speed milk pumps save a lot of energy by adjusting the speed of
milk through the lines. When teamed with an in-line cooler, the variable-speed
pump can maximize precooling by slowing the milk's speed through the cooler.
This allows more time to transfer heat to the well water. Your
WPS Agricultural Consultant can give you more
details about variable-speed pumps.
Back to top
Pays for itself in about two years
The money saved by installing an in-line cooler depends on several factors
such as herd size, number and size of compressors, type of Freon used, and the
age of the bulk tank. WPS estimates that the investment
can pay for itself in as little as two years.
Use the milk precooler calculator
to show how you can save on energy costs by using a milk precooler.
Back to top
For more information
To learn more about how in-line cooling can help you reduce the cost of
cooling milk, call WPS at 877-444-0888.
You may want to ask about additional energy-saving measures that can help you realize
higher profits on your dairy operation.
Back to top